- Operation: automatic, PLC controlled
- Utilities: For the production of 1,000 Nm³/h H2 from natural gas the following Utilities are required:
- 380-420 Nm³/h natural gas
- 900 kg/h boiler feed water
- 28 kW electric power
- 38 m³/h cooling water *
- * can be substituted by air cooling
- By-product: export steam, if required
Video
Hydrogen production from natural gas is to perform the chemical reaction of pressurized and desulfurized natural gas and steam in a special reformer filling with catalyst and generate the reforming gas with H₂, CO₂ and CO, convert the CO in the reforming gases to CO₂ and then extract qualified H₂ from the reforming gases by pressure swing adsorption (PSA).
The Hydrogen Production Plant design and equipment selection results from extensive TCWY engineering studies and vendor evaluations, with especially optimizing the following:
1. Safety and Ease of operation
2. Reliability
3. Short equipment delivery
4. Minimum field work
5. Competitive capital and operating costs
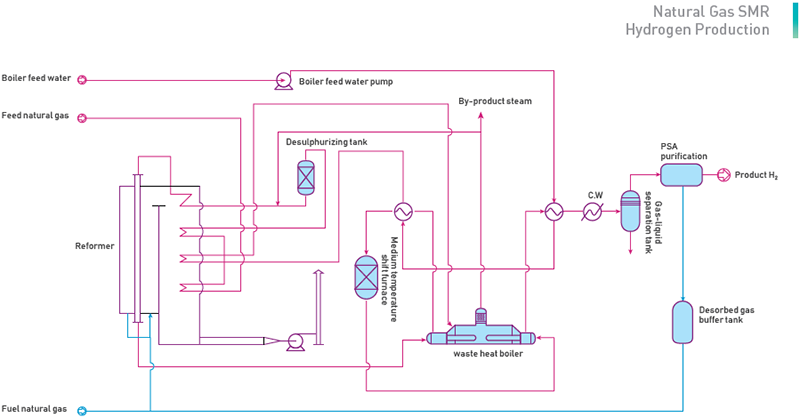
(1) Natural Gas Desulfurization
At a certain temperature and pressure, with the feed gas through the oxidation of manganese and zinc oxide adsorbent, the total sulphur in the feed gas will be off below 0.2ppm below to meet the requirements of the catalysts for steam reform.
The main reaction is:
COS+MnO |
MnS+H2O |
H2S+ZnO |
(2) NG Steam Reforming
Steam reforming process uses water vapour as the oxidant, and by the nickel catalyst, the hydrocarbons will be reformed to be the raw gas for producing hydrogen gas. This process is endothermic process which demands the heat supply from the radiation section of Furnace.
The main reaction in the presence of nickel catalysts is as follows:
CnHm+nH2O = nCO+(n+m/2)H2 |
CO+H2O = CO2+H2 △H°298= – 41KJ/mol |
CO+3H2 = CH4+H2O △H°298= – 206KJ/mol |
(3) PSA Purification
As the process of chemical unit, PSA gas separation technology has been rapidly developing into an independent discipline, and more and more widely applied in fields of the petrochemical, chemical, metallurgy, electronics, national defence, medicine, light industry, agriculture and environmental protection industries, etc. At present, PSA has become the main process of H2 separation which it has been successfully used for purification and separation of carbon dioxide, carbon monoxide, nitrogen, oxygen, methane and other industrial gases.
The study finds that some solid materials with good porous structure can absorb the fluid molecules, and such absorbent material is called the absorbent. When the fluid molecules contact solid adsorbents, the adsorption occurs immediately. The adsorption results in the different concentration of the absorbed molecules in the fluid and on the absorbent surface. And the adsorbed molecules by the absorbent will be enriched on its surface. As usual, different molecules will show different characteristics when absorbed by the adsorbents. Also the external conditions such as fluid temperature and concentration(pressure)will directly affect this. Therefore, just due to this kind of different characteristics, by change of the temperature or pressure, we can achieve the separation and purification of the mixture.
For this plant, various adsorbent are filled in the adsorption bed. When the reforming gas (gas mixture) flows into the adsorption column (adsorption bed) under a certain pressure, due to the different adsorption characteristics of H2, CO, CH2, CO2, etc. the CO, CH2 and CO2 are adsorbed by the adsorbents, while H2 will flow out from the top of the bed to get qualified product hydrogen.